Published
by Rogers Corporation
Enclosure Institute, Elastomeric Material Solutions
Welcome back to the Enclosure Institute™, where we explore best practices for designing reliable, high-performance enclosures.
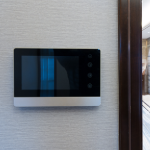
In this case study, we’ll walk through a real-world example where Marian and Rogers worked together to develop a custom sealing solution after a customer’s original gasket design fell short of performance expectations.
Customer Problem
A global designer and manufacturer of intercommunication devices faced a critical leak issue in one of their products. Their communication system’s digital display interface required a gasket to seal the intercom console from dust, moisture, and other contaminants.
However, the original gasket from another manufacturer failed during routine cleaning, allowing liquid cleaning solution to seep into the system. This exposure to moisture compromised internal components, increasing the risk of performance issues over time.
Design Requirements
The customer needed a high-performance sealing solution that:
- Provided a reliable seal against dust, moisture, and liquid cleaning agents
- Maintained strong adhesion to keep the gasket securely in place
- Helped prevent bacterial growth despite frequent use
The Solution
To address the complex challenge of designing a high-performance gasket for an environment prone to moisture and microbial contamination, the team at Marian leveraged their expertise in precision converting in collaboration with Rogers’ material specialists. This partnership aimed to develop a solution that not only met but exceeded the functional requirements of sealing performance and durability.
Let’s review the critical steps in the material selection process:
- Sealing Material: In developing a sealing solution for high-moisture environments, it was crucial to select a material that excels in water and chemical resistance while maintaining integrity over time. Rogers PORON® AquaPro® 4701-41 foam was chosen for its superior sealing capabilities and durability. Its engineered cellular structure ensures robust performance and resilience in challenging conditions, making it ideal for the application's rigorous demands
- Surface Protection: In environments where hygiene is critical, particularly in high-touch medical or industrial settings, it is essential to minimize microbial contamination on device surfaces. To meet this need, a surface protection solution was required that could actively inhibit bacterial growth. An antimicrobial film, a textured, hard-coated polyester film, was selected for its ability to disrupt bacterial growth on contact. This integration not only enhances the gasket’s functionality but also provides a proactive approach to maintaining surface hygiene.
- Adhesive Layer: In ensuring the integrity and performance of the seal over time, it is essential to choose an adhesive that could provide a secure bond between the sealing material (PORON AquaPro 4701-41 in this case) and the molded plastic housing of the intercom unit. For this purpose, 3MTM 9832+ double-coated tape was selected due to its strong adhesion qualities. This adhesive layer completes the assembly by firmly anchoring the components together, crucial for maintaining the seal’s effectiveness in demanding conditions.
Rapid Prototyping and Testing
With the material selection process complete, Marian’s team quickly produced material samples and laser-cut prototypes within 24 hours for evaluation and testing. With immediate access to Rogers’ high-performance materials, Marian’s global network of converting locations allows customers to get quick-turn prototypes and production-ready parts in no time.
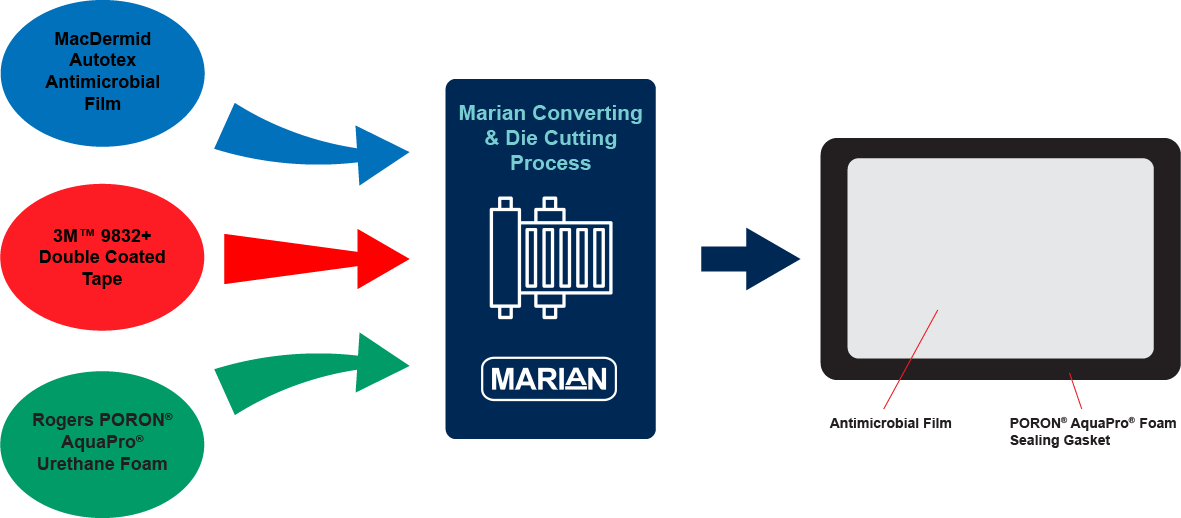
Result
- Faster Prototyping, Faster Validation – With immediate access to Rogers' high-performance materials and Marian’s precision laser-cutting capabilities, the customer received material samples and functional prototypes within 24 hours. This fast turnaround allowed for quicker testing, validation, and design refinements, reducing time to market.
- Reliable, Proven Performance – The custom gasket solution eliminated leaks and provided enhanced durability, ensuring the intercom unit remained protected against moisture, contaminants, and cleaning agents. This improvement significantly reduced the risk of performance issues over time.
- The Right Materials with the Right Converter– By combining Rogers’ high-performance materials with Marian’s precision converting, the final solution outperformed previous gasket designs in sealing effectiveness, durability, and longevity.
- Simplified Sourcing and Exclusive Access - The customer simplified material selection and sourcing by working with Marian, a Rogers Preferred Converter. This partnership provided exclusive access to industry-leading materials like PORON® and BISCO®, ensuring higher quality solutions that aren't readily available in the market.
Key Considerations for your Design
Choosing the right sealing solution requires careful evaluation of material performance, manufacturing efficiency, and long-term reliability. Here are a few things to consider:
- Evaluate and Address Specific Needs: Identify critical performance criteria for your sealing solutions, such as resistance to moisture, durability against cleaning agents, and microbial contamination control. Tailor your material selection to meet these specific requirements to ensure long-term reliability.
- Choose the Right Materials: Opt for materials that not only meet the application's functional demands but also enhance the overall performance.
- Maximize Efficiency with the Right Converter: Working with a converter that utilizes advanced manufacturing technologies, such as laser-cutting, is essential for rapid prototyping and streamlined testing. These capabilities not only accelerate the development process but also allow for quick adjustments and validations, facilitating a smoother and faster transition from design to production. Ensure your converter can deliver quick-turn prototypes, which are crucial for effective testing and timely progression of projects, enhancing overall project efficiency and outcome.
- Partner with Experts: Collaborate with experienced materials and converting specialists to harness their expertise in developing customized sealing solutions. Such partnerships can enhance design efficiency, improve material access, and ensure high-performance outcomes.
By focusing on these key areas, designers can improve the performance and reliability of their enclosure solutions, ensuring they meet both current and future needs effectively.
Master Enclosure Sealing with the Marian and Rogers Enclosure Institute™
Sealing challenges can make or break an enclosure’s performance. Whether you're designing for environmental protection, long-term reliability, or compliance with industry standards, selecting the right materials and understanding effective sealing strategies are critical. That’s why Marian Inc. and Rogers Corporation have partnered to bring you the Enclosure Institute™ — a free learning platform designed to help engineers navigate the complexities of enclosure sealing.
Why Sign Up for the Enclosure Institute™?
Gain exclusive access to:
- Four expert-led modules with in-depth videos, allowing you to learn at your own pace
- Checklists, resources, and tools to guide your enclosure design process
- Actionable insights into real-world sealing challenges
- Certification and an Enclosure Institute Essentials Kit upon completion, recognizing your expertise
The Enclosure Institute™ is designed for engineers at all levels, whether you're new to enclosure sealing or looking to refine your expertise.
Enroll today to take the next step in mastering enclosure design:
Sign Up
Not ready to enroll yet?
Explore more blogs on enclosure design best practices:
Your Trusted Partners in Sealing
With nearly 200 years of material expertise, 70 years of fabrication development, decades of partnership, and thousands of applications designed together, Marian and Rogers bring unmatched knowledge to enclosure sealing. By combining Rogers’ high-performance materials with Marian’s precision converting capabilities, we deliver custom-engineered solutions that enhance durability, reliability, and performance.
Whether you need expert guidance, high-quality materials, or precision-fabricated components, our partnership ensures your enclosures meet the highest industry standards while optimizing efficiency and cost-effectiveness.
Contact Marian
If you have a specific enclosure challenge and need expert guidance, Marian’s team is ready to help. Contact Marian directly for tailored recommendations and support.
Published on Jul 09, 2025
Return to Blog